Chemical transportation is critical to many industries, ensuring that various substances reach their destinations safely and efficiently. However, handling and transporting chemicals have inherent risks that must be managed appropriately to prevent accidents, injuries, and environmental damage. Understanding the dos and don’ts of chemical transportation is essential for maintaining safety and compliance throughout the supply chain.
This blog will explore the critical practices and pitfalls to avoid when transporting chemicals, helping industry professionals navigate this complex process with confidence and responsibility.
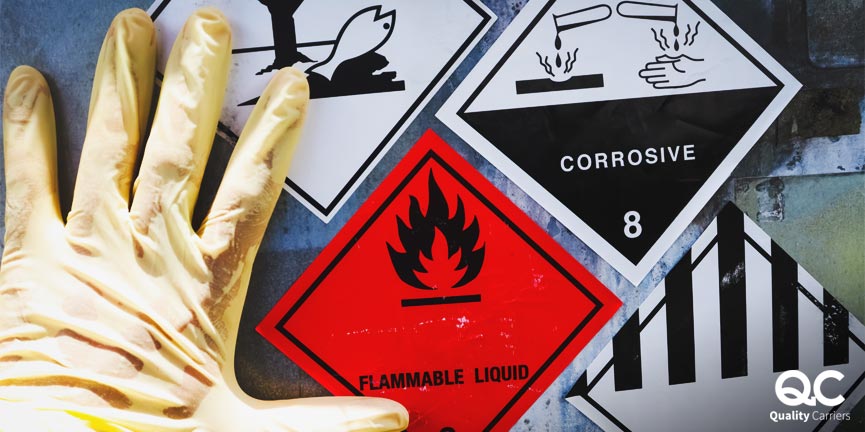
The DO’s of Safety Chemical Transportation
1. Know Your Product Before You Book Your Load
Understanding the characteristics, hazards, and special requirements of the chemical products you transport is crucial for ensuring safe handling and transportation. This includes knowing the chemical composition, physical properties, potential hazards, and any regulatory requirements associated with the product.
2. Make Sure You Give All the Proper Information to Your Broker and Carrier
Providing accurate and comprehensive information about the chemical products to your freight broker and carrier is essential for proper planning and risk assessment. This includes the chemical name, UN number, hazard classification, quantity, packaging requirements, and special handling instructions or precautions.
3. Ensure That You Are Prepared for an Emergency with Extra Stock
Being prepared for emergencies is paramount when transporting hazardous chemicals. Keep a sufficient supply of emergency response equipment and spill containment materials readily available during transportation. This includes absorbent pads, neutralizing agents, personal protective equipment (PPE), spill kits, fire extinguishers, and emergency contact information. Extra stock ensures prompt and effective response in spills, leaks, or other emergencies, minimizing potential risks and environmental impact.
4. Use a Freight Broker to Find Your Carriers
Utilizing a reputable freight broker can streamline finding reliable carriers for transporting chemical products. Freight brokers have access to various networks of carriers and can help match your specific transportation needs with carriers that meet regulatory requirements and safety standards. It’s essential to thoroughly vet carriers to ensure they have the necessary permits, insurance, and experience handling hazardous materials. Verify their compliance with safety regulations and assess their track record for reliability and adherence to safety protocols.
5. Install Bunding and Bunded Storage
Bunding refers to constructing a secondary containment system around chemical storage areas or transport vessels to prevent spills or leaks from spreading and causing environmental contamination. Bunded storage involves containers or tanks with integrated secondary containment features, such as raised edges or walls, to contain any spills or leaks within the designated area. Installing bunding and using bunded storage facilities helps mitigate the risks associated with chemical transportation by providing additional protection against potential spills, leaks, or accidents.
6. Segregate Incompatible Chemicals
Proper segregation of incompatible chemicals is essential for preventing hazardous reactions, spills, or contamination during transportation. Segregation involves storing or transporting different types of chemicals separately to avoid potential interactions that could lead to fires, explosions, or releasing toxic gases. Chemicals should be segregated based on compatibility, as determined by their chemical properties, reactivity, and potential hazards. Implementing transparent segregation practices and labeling systems helps minimize the risk of accidents and ensures personnel safety and the environment.
7. Display Correct DG and Hazard Signage
Correctly displaying Dangerous Goods (DG) and hazard signage ensures the safe transportation of chemicals. DG signage provides essential information about the contents of containers, including the type of chemical, potential hazards, and emergency response procedures. It helps emergency responders, handlers, and other personnel safely identify and handle hazardous materials. Following regulatory requirements, displaying correct DG and hazard signage enhances visibility and awareness, reducing the risk of accidents, spills, or mishandling during transportation.
8. Install Compliant Dangerous Goods Storage
Installing compliant dangerous goods storage facilities is essential for securely storing chemical products and ensuring regulatory compliance. These storage facilities are designed to meet safety standards and regulations for handling hazardous materials. They feature appropriate containment measures, ventilation systems, and safety equipment to prevent spills, leaks, or environmental contamination. Compliant dangerous goods storage facilities also incorporate fire suppression systems, emergency response protocols, and access controls to mitigate risks and protect personnel, property, and the environment. Regular inspection, maintenance, and following safety protocols are essential for effectively managing dangerous goods storage facilities.
9. Always Wear Appropriate Personal Protective Equipment (PPE)
When handling chemicals during transportation, wearing appropriate personal protective equipment (PPE) is crucial to minimize exposure and injury risk. PPE includes gloves, goggles, respirators, protective clothing, and footwear, depending on the specific chemical being handled and the nature of the task. Chemicals may pose various hazards, including skin irritation, respiratory issues, or toxic fumes. Therefore, assessing the potential risks associated with each chemical is essential and ensuring that the appropriate PPE is worn to provide adequate protection for personnel involved in transportation operations is necessary.
10. Use The Appropriate Tools and Equipment
Utilizing the correct tools and equipment is essential for safely handling and transferring chemicals during transportation. Specialized equipment, such as pumps, hoses, spill containment kits, and chemical transfer systems, should be used to minimize the risk of accidents.
It’s important to select tools and equipment compatible with the type of chemical transported and designed to meet safety standards and regulatory requirements. Regular inspection, maintenance, and equipment calibration are necessary to ensure proper functionality and reliability during chemical transportation operations. Additionally, personnel should receive adequate training on the safe use of tools and equipment to mitigate risks and promote safety awareness in chemical transportation activities.
The DON’Ts of Safety Chemical Transportation
1. Don’t Book a Load Without Sharing the Required Details with the Carrier
Providing all necessary information about the chemical product being transported to the carrier is essential. Failing to disclose crucial details such as chemical composition, hazards, handling requirements, and emergency procedures can lead to misunderstandings or inadequate preparation, increasing the risk of accidents or incidents during transportation.
2. Don’t Book a Load Without Understanding Your Product
Before scheduling transportation for chemical products, it is imperative to have a thorough understanding of the properties, hazards, and safe handling procedures associated with the specific chemicals. Lack of knowledge about the product can result in improper handling, storage, or emergency response measures, posing significant risks to personnel, the environment, and public safety.
3. Don’t Hire a Carrier Without Finding Out Their Reputation
When selecting a carrier for chemical transportation, conducting thorough research is essential to assess its reputation, track record, and compliance with safety regulations. Hiring a carrier without verifying their credentials, safety practices, and past performance can expose your organization to unnecessary risks, including delays, accidents, or regulatory violations. Prioritize carriers with a proven reputation for reliability, safety protocol adherence, and emergency responsiveness.
4. Don’t Get Blindsided by Supply Chain Interruptions
It’s crucial to anticipate potential disruptions in the supply chain and have contingency plans to mitigate their impact. Weather conditions, road closures, regulatory changes, or unforeseen incidents can disrupt transportation schedules and jeopardize chemical shipments. By identifying potential risks, you can minimize the likelihood of supply chain disruptions and maintain the integrity and safety of chemical transportation operations.
5. Don’t Put All Your Loads in One Carrier
Relying solely on a single carrier for chemical transportation can increase vulnerability to operational disruptions and limit flexibility in responding to changing circumstances. Diversifying your carrier base and establishing relationships with multiple reputable carriers can enhance resilience and provide alternative options in case of carrier-specific issues, capacity constraints, or service disruptions. By distributing transportation responsibilities across different carriers, you can reduce reliance on any single provider and ensure continuity of service even in challenging situations.
6. Don’t Leave Chemicals Unattended. Clean Up After Spills and Leaks
This rule underscores the importance of proper chemical storage and supervision to prevent accidents or misuse. Leaving chemicals unattended can increase the risk of spills, leaks, or unauthorized access, leading to potential injuries, environmental contamination, or property damage. By ensuring chemicals are securely stored and monitored at all times, individuals can mitigate the risks associated with their presence and maintain a safe working environment.
Prompt and thorough chemical spill and leak clean-up is essential to prevent environmental contamination, protect personnel safety, and comply with regulatory requirements. Neglecting to address spills promptly can lead to environmental damage, health hazards, and regulatory penalties. Establishing effective spill response procedures, providing appropriate spill containment equipment, and training personnel on spill response protocols are essential measures to minimize the impact of spills and mitigate associated risks during chemical transportation operations.
7. Don’t Overlook Risks Associated with Handling and Transfer Tasks
This means not ignoring or neglecting the potential dangers of handling and transferring chemicals. It’s crucial to be aware of the hazards and risks associated with these tasks, such as exposure to toxic substances, chemical spills, or accidents during transportation. By recognizing these risks, appropriate safety measures can be implemented to mitigate them and ensure the safe handling and transfer of chemicals.
8. Don’t Forget to Replace, Update or Maintain Signage
This emphasizes maintaining accurate and visible chemical transportation and storage signage. Signage, such as labels indicating the type of chemicals being transported or stored, hazard warnings, and safety instructions, plays a crucial role in communicating information and alerting individuals to potential risks. Forgetting to replace, update, or maintain signage can lead to confusion, misinformation, and increased risks of accidents or incidents.
9. Don’t Allow Poor Housekeeping Practices
This highlights the necessity of maintaining cleanliness, organization, and orderliness where chemicals are handled, stored, or transported. Poor housekeeping practices, such as cluttered workspaces, improper storage of chemicals, or failure to clean up spills promptly, can create hazardous conditions and increase the likelihood of accidents, injuries, or environmental contamination. Enforcing proper housekeeping procedures to minimize risks and maintain a safe working environment is essential.
10. Don’t Eat, Drink, or Smoke Near Chemicals
This rule emphasizes the importance of preventing potential ingestion, inhalation, or absorption of harmful chemicals. Consuming food or beverages or smoking in areas with chemicals can lead to accidental exposure or contamination, posing severe health risks. By strictly adhering to this guideline, individuals can minimize the chances of chemical ingestion or inhalation, ensuring their safety and well-being.
In conclusion, adhering to the dos and don’ts of chemical transportation is crucial. It safeguards the well-being of workers, protects the environment, and maintains regulatory compliance. By following best practices, such as proper handling procedures, adequate training, and meticulous planning, chemical transport companies can minimize risks and ensure the safe and secure transport of chemicals. Additionally, staying informed about industry regulations and implementing robust safety measures will help mitigate potential hazards and foster a culture of responsibility within the chemical transportation sector.
DOs and DON’Ts of Chemical Transportation FAQs
Proper training ensures that personnel understand the hazards of different chemicals, know how to handle them safely and respond effectively to emergencies. It also helps prevent accidents, injuries, and environmental incidents during transportation.
Common mistakes include:
Inadequate packaging or labeling.
Improper container loading or securing.
Failure to comply with regulatory requirements.
These errors can lead to spills, leaks, or accidents that endanger personnel and the environment.
When transporting hazardous chemicals by road, it’s essential to comply with regulations governing vehicle placarding, driver qualifications, and emergency response procedures. Additionally, drivers should undergo training in handling hazardous materials and equipped with appropriate safety gear.
To ensure the integrity of chemical containers, companies should use suitable packaging materials designed to withstand the properties of the chemicals being transported. Regular inspections, maintenance, and testing of containers are also essential to prevent leaks or ruptures during transit.
Emergency response plans outline procedures for addressing spills, leaks, fires, or other accidents involving hazardous chemicals during transportation. By having a well-defined plan and conducting regular drills, companies can minimize the impact of incidents and protect personnel and the environment.