In this video, Randy, the president of Quality Carriers, provides a detailed recap of his “Pennsylvania 6-5000” tour, named after the famous Glenn Miller song, as it takes him through critical company operations in Pennsylvania. The tour includes four stops, showcasing different aspects of Quality Carriers’ business and its ongoing improvements.
The first stop is in Ono, Pennsylvania, home to a long-standing operation formerly known as JP Donmyer. Quality Carriers took over this location five years ago. This location focuses on dry bulk work, such as chemical ingredients and cement production. Randy highlights the investment in this terminal, which includes a four-bay maintenance shop and a safety school for new drivers. He also mentions a forthcoming on-the-job training center. He notes the efficiency of the operation, which is led by experienced employees. Key leaders include Steve, the regional fleet manager, and Pete, the local shop manager.
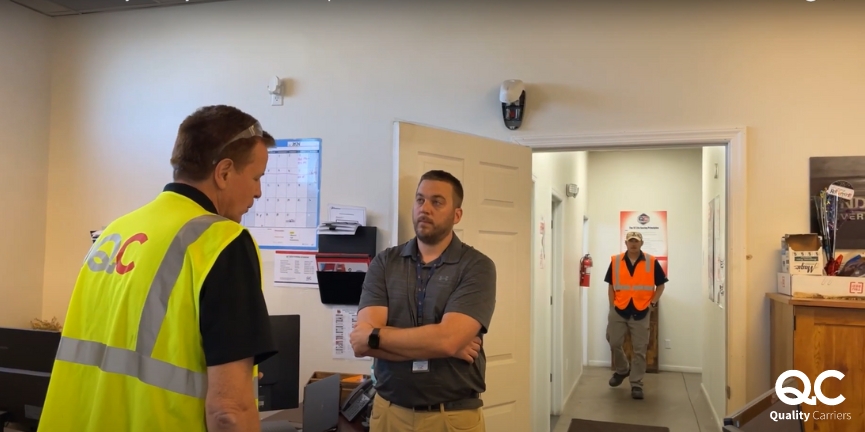
Shortly after the Little League World Series, the second stop brings Randy to Williamsport, Pennsylvania. This terminal also handles dry bulk work, and Randy speaks with the local team, including Kris, a regional terminal manager (RTM), and Jeff, a senior fleet manager. The mechanics team plays a vital role in maintaining the fleet. Randy is impressed by the long-standing team members and their dedication to keeping operations running smoothly.
Next, Randy visits Parryville, where Quality Carriers manages about ten drivers. These drivers focus on moving dry bulk materials like sand, fly ash, and coal for power plants. He meets with terminal manager Diane Heckman and her husband, Glenn, who manages the shop. Glenn is known for his creativity, having developed an oil evacuation system that improves safety and efficiency, which is being implemented across the company’s shops. The terminal’s shop team is skilled in various repair and modification tasks, from welding to rebuilding equipment. This makes it a key location for Quality Carriers’ maintenance efforts.
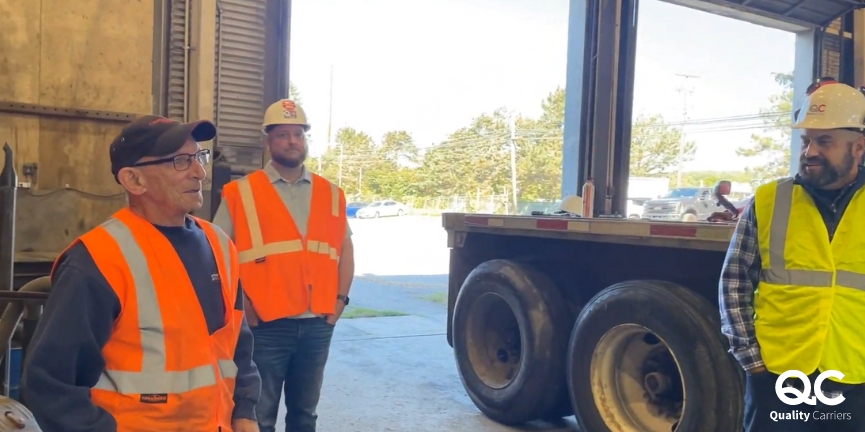
The final stop on the tour is in Stockertown, near Allentown and Nazareth, Pennsylvania. This site services a significant customer in the cement industry with a small but efficient team. Randy meets with Adam, the regional terminal manager, and other staff like Margie and Cheryl, who oversee the terminal’s operations. He also tours the customer’s cement-making facility, which reminds him of his manufacturing background. The stop concludes with a visit to the terminal’s shop, where Randy meets long-time employees like Butch, a part-time mechanic with over 50 years of experience.
Overall, the “Pennsylvania 6-5000” tour showcases Quality Carriers’ commitment to safety, efficiency, and innovation. It highlights the dedicated teams and upgraded facilities that drive the company’s success in the dry bulk industry. Randy appreciates the hospitality he received at each location and looks forward to future tours.
Frequently Asked Questions
Dry bulk transportation, involving materials like cement, sand, and coal, requires specialized equipment. It also demands different handling procedures compared to liquid chemical hauling. Dry bulk loads are often non-liquid powders or granular materials that must be transported in sealed containers to prevent contamination or loss. Loading and unloading dry bulk materials require specific skills and equipment. Therefore, Quality Carriers invests in specialized training for its drivers and terminal staff.
Terminal managers at Quality Carriers are pivotal to the smooth functioning of daily operations. They oversee everything from driver schedules to equipment maintenance, ensuring that deliveries are made on time and comply with safety standards.
Fleet maintenance is a critical component of Quality Carriers’ operations. They maintain a network of maintenance shops staffed by experienced mechanics. Each terminal’s shop is equipped to handle a variety of services, from routine maintenance to complex repairs. This ensures that the fleet is always kept in top condition. Additionally, Quality Carriers continuously invests in new technology and equipment to improve maintenance efficiency and environmental compliance across all terminals.